In 3D cảm biến cho các vệ tinh
Các nhà khoa học của MIT đã sáng tạo ra các cảm biến plasma đầu tiên ở quy mô sản xuất hoàn toàn bằng số hóa cho các tàu vũ trụ quay quanh quỹ đạo. Các cảm biến plasma đó được biết như các máy phân tích tiềm năng trễ (retarding potential analyzers RPAs), đã được sử dụng cho các vệ tinh để xác định thành phần hóa học và phân bố năng lượng ion trong bầu khí quyển.
Phần cứng in 3D và cắt laser triển khai như các cảm biến plasma bán dẫn tiên tiến đều được chế tạo trong phòng sạch, khiến chúng trở nên đắt đỏ và đòi hỏi một quá trình phức tạp diễn ra trong nhiều tuần. Trái ngược với quá trình này, các cảm biến in 3D chỉ mất vài chục đô la và giảm thời gian sản xuất xuống còn vài ngày.
Do quá trình sản xuất chi phí thấp và diễn ra nhanh hơn, các cảm biến này lý tưởng cho CubeSats. Các vệ tinh giá rẻ, ít tốn điện và khối lượng thấp thường được sử dụng cho giám sát truyền thông và môi trường ở thượng tầng khí quyển trái đất.
Các nhà nghiên cứu đã phát triển RPAs bằng việc sử dụng vật liệu gốm thủy tinh có độ bền lớn hơn nhiều so với các vật liệu làm cảm biến thông thường như silicon và các lớp phủ màng mỏng. Bằng việc sử dụng gốm thủy tinh trong quá trình chế tạo đã được phát triển cho in 3D với nhựa, chúng có khả năng tạo ra các cam biến ở các hinh dạng phức tạp có thể chống chịu ở dải nhiệt độ rộng ở một tàu vũ trụ có thể bay ở quỹ đạo thấp của trái đất.
“Việc sản xuất đắp bồi có thể tạo ra sự khác biệt trong tương lai của phần cứng thiết bị vũ trụ. Một số người cho là khi bạn in 3D cái gì đó, bạn phải làm ra thứ hiệu suất hoạt động thấp đi. Tuy nhiên chúng tôi đã chứng tỏ không phải lúc nào cũng xảy ra trường hợp đó, thi thoảng không phải đánh đổi gì cả”, theo nhận xét của Luis Fernando Velásquez-García, một nhà nghiên cứu chính ở Các phòng thí nghiệm Công nghệ các hệ vi mô ở MIT (MTL) và là tác giả chính của bài báo về các cảm biến plasma.
Tham gia nghiên cứu cùng với Velásquez-García trong công trình này còn có tác giả thứ nhất, postdoc MTL Javier Izquierdo-Reyes, học viên Zoey Bigelow, postdoc Nicholas K. Lubinsky. Nghiên cứu được xuất bản trên Additive Manufacturing.
Các cảm biến linh hoạt
Một cảm biến RPA từng được sử dụng lần đầu tiên trong một nhiệm vụ vũ trụ vào năm 1959. Cảm biến này đã dò được năng lượng của các ion, hay các hạt tích điện, trôi nổi trong plasma, vốn là một hỗn hợp ở trạng thái siêu nóng của các phân tử có trong thượng tầng khí quyển trái đất. Trên một tàu vũ trụ bay trong quỹ đạo như CubeSat, các thiết bị linh hoạt này đo đạc năng lượng và thực hiện các phân tích hóa học trực tiếp, qua đó có thể giúp các nhà khoa học dự báo dược thời tiết hoặc giám sát biến đổi khí hậu.
Các cảm biến này chưa một loạt các lưới tích điện được điểm các lỗ rỗng nhỏ. Khi plasma di chuyển qua các lỗ rỗng này, các electron và các hạt khác bị tách ra cho đến khi chỉ còn các ion. Các ion này tạo ra một dòng điện mà các cảm biến có thể đo đạc và phân tích.
Vấn đề chính dẫn đến thành công của một RPA là một cấu trúc phù hợp cho các mắt lưới. Nó phải cách điện trong khi có khả năng phù hợp với sự thay đổi đột ngột nhiệt độ. Các nhà nghiên cứu thường sử dụng một loại vật liệu gốm thủy tin có thể in được để đạt được các đặc tính đó, Vitrolite.
Được tìm ra trong đầu thế kỷ 20, Vitrolite thường được sử dụng để làm các loại ngói màu sắc để cho các công trình art deco.
Vật liệu có độ bền cao này có thể phù hợp với nhiều mức nhiêt độ như 800 độ C mà không bị hư hỏng, trong khi các polymer được sử dụng trong RPAs bán dẫn có thể bị chảy ở mức nhiệt 400 độ C.
“Khi anh chế tạo cảm biến này trong một phòng sạch, anh không có mức nhiệt độ tương tự ở bên ngoài để tinh chỉnh các loại vật liệu và cấu trúc và các chúng tương tác với nhau. Những gì khiến cho nó trở thành có thể là nhờ những phát triển mới nhất của công nghệ đắp bồi”, Velásquez-García says.
Nghĩ lại về quá trình chế tạo
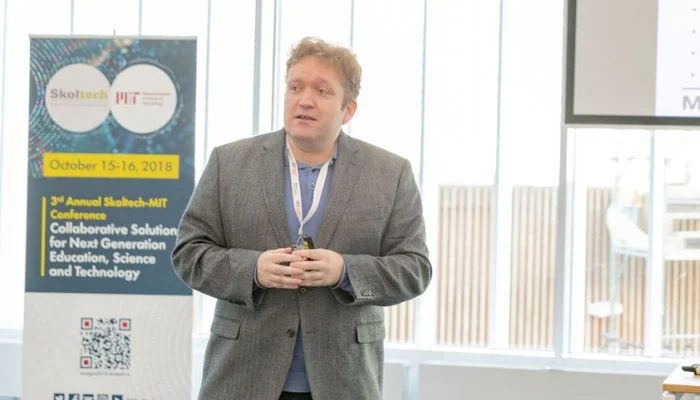
Quá trình in 3D với vật liệu gốm, cụ thể là các bột gốm, là việc dùng một laser để nung nó thành các hình dạng mong muốn nhưng quá trình này thường khiến vật liệu này thô và tạo ra các điểm yếu do mức nhiệt cao từ laser.
Thay vào đó, các nhà nghiên cứu của MIT đã sử dụng kỹ thuật polymer hóa bằng tia cực tím, một quá trình đã được áp dụng hàng thập kỷ trước nền sản xuất bằng công nghệ đắp bồi với các polymer hay nhựa thông. Với polymer hóa bằng tia cực tím, một cấu trúc 3D được chế tạo một lớp tại thời điểm được phủ kín bằng một vật liệu lỏng, trong trường hợp này là Vitrolite. Tia cực tím được dùng để xử lý vật liệu sau mỗi lớp được bồi thêm, và sau đó nền tảng này lại được chiếu tia cực tím một lần nữa. Mối lớp có độ dày 100 micron (xấp xỉ đường kính sợi tóc người), cho phép tạo ra các hình dạng gốm phức tạp, nhẵn và không bị xốp.
Trong nền sản xuất số hóa, các vật thể được miêu tả trong một tập thiết kế hết sức phức tạp. Sự chính xác này cho phép các nhà khoa học tạo ra lưới cắt laser với các hình dạng độc đáo, vì vậy các lỗ được xếp theo dòng một cách hoàn hảo khi chúng được thiết kế ở bên trong RPA. Điều này cho phép có thêm nhiều ion di chuyển qua, dẫn đến các đo đạc có độ phân giải cao hơn.
Bởi vì các cảm biến đều rẻ để sản xuất và có thể được chế tạo trong thời gian ngắn, nhóm nghiên cứu đã làm mẫu thử theo bốn thiết kế độc đáo.
Trong khi một thiết kế có hiệu quả đặc biệt trong việc bắt và đo đạc một dải rộng plasma, như một vệ tinh có thể bắt gặp trong một vũ trụ, thiết kế khác phù hợp với cảm biến trong các plasma vô cùng đậm đặc và lạnh, thường chỉ có thể đo đạc được bằng việc sử dụng các thiết bị bán dẫn siêu chính xác.\
Độ chính xác cao này có thể cho phép ứng dụng các cảm biến in 3 D trong nghiên cứu năng lượng nhiệt hạch hoặc máy bay siêu thanh. Quá trình làm mẫu nhanh này có thể đem lại nhiều đổi mới sáng tạo trong thiết kế vệ tinh và tàu vũ trụ, Velásquez-García cho biết thêm.
“Nếu anh muốn có được đổi mới, anh cần phải chấp nhận độ rủi ro. Công nghệ đắp bồi là một công nghệ hoàn toàn khác biệt để chế tạo phần cứng thiết bị không gian. Tôi có thể tạo ra phần cứng thiết bị không gian và nếu có thất bại, nó không phải là vấn đề gì ghê gớm bởi tôi có thể làm phiên bản mới rất nhanh và giá thành thấp, và thực sự dễ tích hợp trên thiết kế ban đầu. Đó là một mô hình sandbox lý tưởng cho các nhà nghiên cứu”, anh nói.
Dẫu hiện tại thì Velásquez-García hài lòng với các cảm biến này, trong tương lai anh vẫn muốn tối ưu quá trình chế tạo. Giảm thiểu độ dày của các lớp hoặc kích thước pixel trong quá trình nhựa hóa bằng tia cực tím vật liệu gốm thủy tinh có thể tạo ra phần cứng phức tạp thậm chí còn có độ chính xác cao hơn nhiều. Tuy nhiên việc sản xuất bằng công nghệ đắp bồi một cách đầy đủ các cảm biến này có thể khiến chúng tương thích với sản xuất thiết bị trong không gian. Anh cũng muốn khám phá việc sử dụng trí tuệ nhân tạo để tối ưu thiết kế cảm biến cho các trường hợp sử dụng đặc biệt, như giảm thiểu khối lượng của chúng trong khi vẫn đảm bảo giữ nguyên chúng về mặt cấu trúc.
Nguyễn Nhàn tổng hợp
Nguồn: https://techxplore.com/news/2022-07-3d-sensors-satellites.html
https://www.automationalley.com/articles/heres-how-researchers-are-3d-printing-sensors-for-satellites